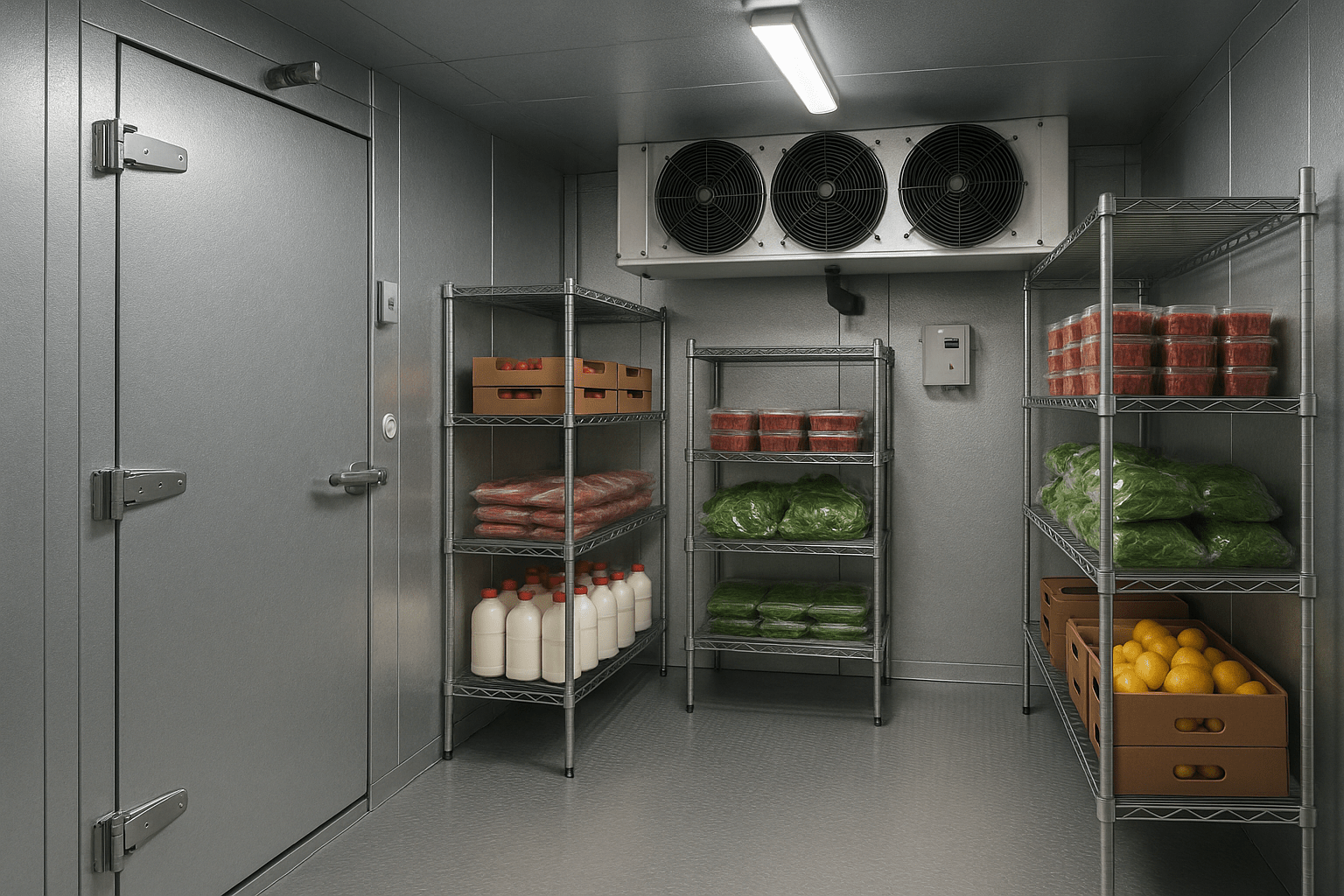
The Complete Guide to Walk-In Cooler Features and Prices
Essential Features of Walk-In Coolers for Business Success
A walk-in cooler is a large, insulated storage space designed to maintain cold temperatures for preserving perishable items. These units serve as critical infrastructure for many businesses requiring temperature-controlled environments.
Quick Walk-In Cooler Facts:
- Temperature Range: Typically operates between 35°F (1.7°C) and 55°F (13°C)
- Standard Sizes: Range from 6'x6' to 12'x12', with custom sizes available
- Lifespan: 15-20 years with proper maintenance
- Primary Components: Insulated panels, door system, refrigeration unit, shelving
- Starting Price: From approximately $4,625 for basic models
Walk-in coolers are essential investments for businesses across multiple industries. Whether you're operating a restaurant, grocery store, floral shop, brewery, or mortuary facility, these refrigerated spaces provide the consistent temperature control needed to maintain product quality and comply with regulations.
"A walk-in cooler can be one of the largest upgrade purchases your business makes," notes industry research, highlighting the importance of selecting the right unit for your specific needs.
The key to finding the ideal walk-in cooler lies in understanding your specific requirements. Consider factors like:
- Your peak storage needs and available space
- Indoor vs. outdoor installation preferences
- Insulation quality (R-values)
- Door types and accessibility requirements
- Flooring options based on usage patterns
With proper selection and maintenance, a walk-in cooler becomes not just a storage solution, but a critical business asset that improves efficiency, reduces waste, and ensures product integrity.
Explore more about walk-in cooler:
Understanding Walk-In Coolers
Ever wondered what makes a walk-in cooler tick? At its heart, it's a spacious, insulated room with a cooling system that keeps everything inside at just the right temperature. Whether you're storing yesterday's prep work or tomorrow's floral arrangements, understanding how these marvels work can help you make the best choice for your business.
Primary Components
Think of a walk-in cooler as a team where every player has an important role. The star players include:
The insulated panels form the walls, ceiling, and sometimes floor of your cooler. These aren't just any panels – they typically feature a hearty 4-inch insulation core sandwiched between metal skins. They lock together with special cam-action devices that create an airtight seal – keeping the cold in and the heat out.
The refrigeration system is the beating heart of any walk-in cooler. This includes the compressor (which pressurizes the refrigerant), the condenser (releasing heat from the refrigerant), the expansion valve (reducing pressure), and the evaporator (absorbing heat from inside).
Your door system might seem simple, but it's engineered with heavy-duty hinges, magnetic gaskets for tight seals, and safety releases to prevent anyone from getting accidentally trapped inside – an important safety feature!
Digital temperature controls keep everything running at precisely the right temperature, while adjustable shelving systems help you make the most of every square inch of storage space.
Refrigeration Cycle Explained
The magic behind your walk-in cooler happens in four main stages:
First comes compression, where the compressor pressurizes refrigerant gas, warming it up in the process. Next is condensation, when that hot gas travels to the condenser and releases its heat, turning into a liquid. During expansion, this liquid refrigerant passes through an expansion valve that reduces its pressure and temperature. Finally, in the evaporation stage, the now-cold refrigerant absorbs heat from inside your cooler through the evaporator, turning back into a gas before heading back to the compressor to start all over again.
As one industry expert puts it, "Heat energy always moves from areas of higher temperature to areas of lower temperature." This fundamental principle is what makes refrigeration possible!
Key Industries and Applications
Walk-in coolers are the unsung heroes across numerous industries. In restaurants, they store everything from fresh ingredients to prepared foods and beverages. Grocery stores rely on them to keep dairy, produce, and other perishables fresh for customers.
Breweries use these coolers to maintain the perfect temperature for storing and aging beer, while floral markets depend on them to extend the life of beautiful cut flowers and arrangements. Food warehouses couldn't function without walk-in coolers for their bulk storage needs.
Here at American Mortuary Coolers, we've seen how walk-in coolers serve vital functions in mortuaries, providing appropriate preservation environments with dignity and reliability. But the applications don't stop there – pharmaceutical companies store temperature-sensitive medications, and educational institutions support their food service operations with these versatile units.
Our nationwide presence – from Johnson City, Tennessee to Los Angeles, California – has given us unique insight into how regional requirements affect walk-in cooler needs. Whether you're dealing with the humidity of the South or the dry heat of the Southwest, we understand that your cooling needs are as unique as your business.
With the right walk-in cooler, you're not just buying a refrigerated box – you're investing in peace of mind and operational excellence for your business, whatever industry you serve.
Key Features and Specifications of Walk-In Coolers
Choosing the right walk-in cooler for your business isn't just about finding a cold box—it's about finding a solution that perfectly aligns with your unique needs. Let's explore the features that truly matter when making this important investment.
Size Options
Walk-in coolers come in all shapes and sizes to fit your specific space and storage requirements. Standard sizes range from compact 6'x6' units perfect for small operations to expansive 12'x12' spaces and beyond for larger facilities.
But here's the thing about cooler sizing—your business isn't standard, so why should your cooler be? At American Mortuary Coolers, we understand this perfectly. We create custom-sized units ranging from 6' to 16' wide and up to a generous 60' in length.
I always remind our clients that an overcrowded cooler is like trying to work in an overstuffed closet—inefficient and frustrating. Make sure to consider your peak storage needs, not just your average day-to-day requirements. Your future self will thank you!
Materials and Construction
The materials used in your walk-in cooler make all the difference in its performance and longevity. Modern coolers feature a sandwich-like panel construction with metal skins on both sides of a thick insulation core, typically 4 inches, all secured with clever cam-action locks that create a tight, energy-efficient seal.
When it comes to the metal finishes, you've got options:
Galvanized steel offers excellent durability at a budget-friendly price point. Aluminum provides a lightweight, naturally corrosion-resistant alternative that many of our clients prefer. If you're looking for the gold standard, stainless steel delivers best strength and corrosion resistance, though it does come with a higher price tag. For a middle-ground option, Galvalume offers improved durability through its protective aluminum and zinc alloy coating.
R-Value Importance
Let's talk about R-values—the unsung hero of cooler efficiency. This simple number measures how well your insulation resists heat flow. Higher numbers mean better insulation, and better insulation means lower energy bills.
Current energy standards require a minimum R-25 for coolers and R-32 for freezers, as established by the Energy Independence and Security Act. These aren't arbitrary numbers—they ensure your unit maintains consistent temperatures without working overtime.
Think of good insulation like a quality winter coat—it keeps the cold in and the heat out, allowing your refrigeration system to work less and last longer. At American Mortuary Coolers, we make sure our units meet or exceed these standards because we know how directly they impact your bottom line.
Doors and Flooring
Your cooler door is more than just an entrance—it's the most frequently used component and a critical factor in energy efficiency. Swing doors (typically 34" x 78") are the standard choice for most installations, offering a good balance of accessibility and insulation. For tight spaces or high-traffic areas, sliding doors provide an excellent alternative. And if you're regularly moving large items in and out, roll-up doors offer unbeatable convenience.
Flooring might seem like an afterthought, but it significantly impacts both performance and durability. Insulated floors can boost energy efficiency by up to 15%—a considerable saving over the life of your cooler. If you're installing directly on a concrete slab, non-insulated options might be suitable. For facilities using heavy equipment like pallet jacks, reinforced flooring is a must-have. And in environments where moisture is common, slip-resistant surfaces provide essential safety.
Refrigeration Systems
The heart of any walk-in cooler is its refrigeration system, which comes in two main configurations:
Self-contained systems package all components into one neat unit—think of them as the "plug and play" option. They're easier to install and maintain, making them ideal for smaller coolers or businesses without dedicated maintenance staff.
Remote systems place the condenser and compressor away from the evaporator. While this requires more complex installation, it reduces noise and heat inside your facility, improves energy efficiency for larger installations, and typically extends component lifespan. It's like moving the noisy part of your air conditioner outside your home—creating a more pleasant environment inside.
These systems come with different mounting options too. Top-mount units save valuable floor space but require clearance above. Side-mount configurations offer easier access for maintenance. Remote mounting reduces noise and heat—perfect for creating a more comfortable workspace.
Walk-In Cooler Insulation Types
The insulation in your walk-in cooler is like the insulation in your home—largely unseen but incredibly important. It directly affects energy efficiency, temperature stability, and ultimately, your operating costs.
Polyurethane insulation stands as the premium choice in modern coolers. It delivers the highest R-value per inch of any commonly used insulation material, excellent moisture resistance when properly encased, and maintains its insulating properties over time with minimal degradation. At American Mortuary Coolers, we prefer foamed-in-place polyurethane because it creates a seamless barrier with consistent performance throughout the entire panel—no weak spots, no surprises.
Extruded polystyrene (XPS) represents an alternative option with good initial insulation properties. However, it's more vulnerable to moisture absorption than polyurethane and research shows it can lose around 20% of its R-value over a decade or more of use. It's like comparing a premium coffee thermos to a standard one—both work, but one will keep things at the right temperature longer.
Most walk-in coolers feature standard 4-inch thick insulation, which meets energy codes while balancing performance with space efficiency. For specialized applications or particularly demanding environments, improved options like 5-3/8 inch panels deliver superior thermal efficiency.
The quality of your insulation directly impacts your bottom line. High-quality insulation reduces compressor runtime, proper sealing prevents cold air leakage, and consistent R-values ensure stable temperatures with minimal fluctuation. As one industry source notes, "Polar King walk-ins are so efficient that they can reduce maintenance & repair costs, cut power bills, and eliminate construction & replacement costs." That's the power of proper insulation.
Walk-In Cooler Doors and Flooring
The doors and flooring of your walk-in cooler might not be the first things you think about, but they're among the features you'll interact with most frequently—and they significantly impact your day-to-day operation.
Your cooler door serves as the gateway between two temperature zones, making its design and features crucial to energy efficiency and convenience. Swing doors remain the most common choice, available in various widths from 36" to 48" and often featuring self-closing hinges and automatic door closers to maintain temperature integrity. Security and safety go hand-in-hand with keyed entry latches and interior safety releases that prevent accidental entrapment.
Sliding doors shine in narrow spaces where swing door clearance is limited. They're particularly valuable in high-traffic areas but require proper sealing to maintain energy efficiency. Many facilities also incorporate strip curtains as a supplementary barrier, reducing cold air loss during frequent entries and exits—these simple additions can help save energy costs by up to 10%.
Beyond the basic door types, consider features that improve durability and convenience: Diamond tread kick plates protect door surfaces from damage, heated door frames prevent condensation and freezing in humid environments, view windows allow visibility without opening the door, and heavy-duty triple hinges support frequent use without sagging.
Here's a pro tip from one maintenance expert: "Close a thin piece of paper in the door. If you can pull it out easily, the seal needs attention." This simple test can reveal issues before they impact your energy bills.
The flooring in your walk-in cooler faces unique challenges, from temperature fluctuations to heavy equipment traffic. Insulated floors can save up to 15% on energy costs and are essential when installing over non-insulated surfaces. They typically feature durable aluminum or stainless steel surfaces to withstand daily use.
For installations directly on properly insulated concrete, a no-floor installation reduces overall height requirements while maintaining efficiency. Facilities using heavy equipment need reinforced flooring with additional structural support and thicker metal surfaces, often including seismic anchoring with galvanized steel backing for stability.
The finishing touches matter too—slip-resistant surfaces improve safety, while vinyl or epoxy coatings simplify cleaning. Food service operations benefit from NSF-compliant materials that meet strict sanitation standards.
At American Mortuary Coolers, we understand the unique demands of mortuary facilities, which is why we offer specialized flooring designed to accommodate mortuary carts while providing easy cleaning and maintaining precise temperature control.
The right combination of doors and flooring ensures your walk-in cooler offers convenient access, energy efficiency, and the durability your specific application demands—turning a simple cold storage space into a seamless extension of your operation.
Indoor vs. Outdoor Walk-In Coolers
Choosing between an indoor or outdoor walk-in cooler is one of the first big decisions you'll make when investing in refrigerated storage. Like choosing between a basement or detached garage, each option comes with its own set of advantages that might make it perfect—or problematic—for your specific situation.
Indoor Walk-In Coolers
Indoor walk-in coolers live inside your existing building, tucked away within your workspace. Think of them as rooms within rooms, offering some significant benefits:
Protected environment means your cooling system doesn't have to fight against scorching summer heat or freezing winter conditions. This protection translates directly into lower energy bills and less wear and tear on your equipment.
Convenient access is another major advantage—your staff won't need to trek outside in bad weather to retrieve items. This proximity can improve workflow efficiency and reduce the time doors stay open during access.
Energy efficiency tends to be better with indoor units since they operate in a more stable temperature environment. Your refrigeration system won't need to work as hard when the surrounding air isn't fluctuating wildly between seasonal extremes.
However, indoor installations do come with some challenges to consider. They consume valuable interior space that might otherwise serve your core business functions. The refrigeration system also releases heat into your surrounding workspace, potentially affecting comfort levels nearby. You'll need to maintain a minimum 2-inch clearance around the unit and ensure proper ventilation for the condensing unit to function correctly.
Outdoor Walk-In Coolers
Stepping outside, outdoor walk-in coolers stand as independent structures adjacent to your main building. These freestanding units offer their own distinct advantages:
Preserving interior space is perhaps the biggest benefit—you won't sacrifice valuable indoor square footage that could be used for serving customers or other revenue-generating activities.
Expansion flexibility comes built-in with outdoor units, as they're typically easier to enlarge or relocate as your business grows. Without building constraints, you can often add sections more readily than with indoor installations.
Noise reduction is a welcome side effect, as the mechanical hum of compressors stays outside rather than contributing to your indoor ambient noise levels.
Delivery accessibility can be optimized with outdoor placement, allowing suppliers to stock your cooler without navigating through your main facility.
Of course, outdoor units face their own challenges. They must be engineered for weather resistance to handle everything from heavy snow to blistering heat. Security concerns may require additional measures like locks, lighting, or cameras. You'll need extended utility connections for power and possibly water, and may face zoning requirements or need special permits depending on your location.
"Powers Equipment mini walk-in coolers and freezers are designed for outdoor use only," notes one manufacturer, highlighting the importance of selecting units specifically engineered for their intended environment.
Placement Considerations
Whether you go indoor or outdoor with your walk-in cooler, thoughtful placement will save you headaches down the road.
Your condensing unit should ideally be installed in a shaded spot with plenty of air circulation—think of it like positioning a pet's bed away from direct sunlight and where fresh air can flow freely. Door clearance needs careful planning to ensure staff can fully open doors and easily move products in and out without awkward maneuvering.
Proximity to utilities matters too—the closer to existing electrical service and drainage, the simpler your installation will be. And don't forget to consider future growth. If your business is likely to expand, leaving space for potential additions could save you from costly relocations later.
At American Mortuary Coolers, we've helped clients from the humid coastal areas of Florida to the dry heat of Arizona select appropriate solutions based on their regional climate challenges. Our nationwide experience means we understand how different environments affect both indoor and outdoor units.
Comparison of Indoor vs. Outdoor Walk-In Coolers
Feature | Indoor Units | Outdoor Units |
---|---|---|
Initial Cost | Generally lower | Typically higher due to weatherproofing |
Energy Efficiency | Better in climate-controlled spaces | May require more energy in extreme climates |
Space Utilization | Consumes interior space | Preserves interior space |
Installation Complexity | Simpler, minimal site prep | More complex, may require foundation work |
Maintenance Access | Convenient, protected environment | Exposed to elements during servicing |
Noise Level Inside Facility | Higher if self-contained | Lower with external compressor |
Security | Protected by building security | May require additional security measures |
Expandability | Often limited by building constraints | Generally easier to expand |
Choosing between indoor and outdoor walk-in coolers isn't just about space—it's about understanding your specific business rhythm, environmental conditions, and growth trajectory. At American Mortuary Coolers, we've designed custom solutions for both settings, ensuring optimal performance whether your cooler lives indoors or braves the elements outside. Our experience with mortuary facilities nationwide has taught us that the right choice varies greatly depending on your unique circumstances.
Energy Efficiency and Cost Savings with Walk-In Coolers
Let's talk about something that affects your bottom line every single day: how much energy your walk-in cooler uses. This isn't just about being environmentally friendly (though that's a nice bonus)—it's about keeping more money in your pocket month after month.
Factors Affecting Energy Consumption
When it comes to energy efficiency, not all walk-in coolers are created equal. Several key elements determine whether your unit will be an energy sipper or guzzler.
1. Insulation Quality
Think of insulation as your cooler's winter coat—the better it is, the less energy needed to stay cold.
A higher R-value means better insulation performance, plain and simple. Those seamless, foamed-in-place polyurethane panels we use at American Mortuary Coolers? They maintain an impressive R-32 rating that prevents heat from sneaking in. Compare that to extruded polystyrene, which can lose up to 20% of its insulating power over time—a bit like a coat that gets thinner every year.
2. Door System Efficiency
Your cooler's door is like the front door of your house—leave it open, and you're basically cooling the outdoors.
Those magnetic gaskets creating an airtight seal aren't just nice to have—they're essential for efficiency. Auto-closers ensure nobody accidentally leaves the door ajar after a busy morning. And those strip curtains you might see in some coolers? They're not just for show—they create a thermal barrier during those inevitable moments when the door needs to stay open.
Door heaters are another clever feature that prevents condensation and frost without wasting energy. It's these seemingly small details that add up to significant savings.
3. Refrigeration System Design
The heart of your walk-in cooler is its refrigeration system, and modern components have come a long way in efficiency.
Those EC (electronically commutated) motors use up to 70% less energy than their older counterparts—that's like switching from an old gas-guzzler to a hybrid car. Demand defrost technology is another game-changer, saving up to 27% on energy by defrosting only when needed rather than on a timer.
"Walk-in coolers not only store perishables but offer significant energy efficiency and extended shelf life," as industry research points out. It's true—a well-designed cooler doesn't just preserve your products; it preserves your budget too.
Real-World Energy Consumption
Let's talk real numbers. A standard 6x6 walk-in cooler typically consumes about 1.08 kWh per month, which translates to around $68.71 at average national electricity rates. Step up to a 10x10 walk-in freezer, and you're looking at approximately 2.04 kWh monthly, or about $145.97.
The good news? Energy-efficient models can slash these costs by 15-30%. That might not sound like much at first, but multiply those savings over years of operation, and you're talking thousands of dollars back in your pocket.
Practical Cost-Saving Tips
Beyond choosing an efficient unit, how you use and maintain your walk-in cooler makes a huge difference. Here are some practical ways to keep those energy bills in check:
Keep your cooler organized like your grandmother's pantry—everything in its place, with room for air to circulate. Blocking those evaporator coils with stored items is like putting a blanket over your air conditioner and wondering why it's not working well.
Regular maintenance isn't just a suggestion—it's essential for efficiency. Those condenser coils need quarterly cleaning (think of them as the radiator of your cooling system). Door seals need checking—a tiny gap can leak surprising amounts of cold air. And just like your car needs the right amount of oil, your cooler needs the proper refrigerant charge.
Be mindful of how you use the cooler. Every door opening lets cold air escape, so plan ahead to minimize trips. Let hot foods cool to room temperature before refrigerating them—your cooler shouldn't double as your cooling system. And those energy-efficient LED lights? They're not just easier on your electric bill; they produce less heat inside your cooler.
At American Mortuary Coolers, we understand that different climates present different challenges. Our nationwide presence—from the humidity of Tennessee to the heat of California—helps us design solutions that work efficiently wherever you are.
By choosing an energy-efficient walk-in cooler and following these common-sense practices, you're not just saving money—you're also reducing your environmental footprint. It's one of those rare situations where doing the right thing for your business also happens to be the right thing for the planet.
For more energy-saving ideas applicable to your cooling systems, check out the Energy-Saving Tips from the Department of Energy.
Installation Requirements and Processes for Walk-In Coolers
Installing a walk-in cooler isn't just about putting pieces together—it's about creating the foundation for years of reliable performance. Whether you're expanding your restaurant or upgrading your mortuary facilities, understanding the installation process helps you prepare properly and avoid headaches down the road.
Site Preparation
Before your shiny new walk-in cooler arrives at your doorstep, you'll need to make sure your site is ready to welcome it.
For indoor installations, you'll need a clean, level concrete floor that can handle the weight of the unit. Think of it like preparing a special place for an important guest—you want the foundation to be solid and welcoming. Your floor should be perfectly level, as even small variations can cause issues with door alignment and panel sealing.
If you're placing your walk-in cooler outdoors, you'll need a concrete pad that extends at least 6 inches beyond the cooler on all sides. This extra space acts as a buffer zone and helps protect your investment from the elements. Don't forget to consider drainage—water pooling around your unit is never a good thing.
Space clearances matter tremendously. Indoor units need breathing room—at least 2 inches of air gap around all sides. If you're installing a top-mounted refrigeration system, leave at least 2 feet of clearance above the unit. And remember that doors need space to swing open fully, so plan your layout accordingly.
"An important consideration is the location of the condensing unit," industry experts point out. "Outdoor installations may require more frequent attention due to exposure to weather and temperature extremes." This is especially true in places with extreme climates, like the scorching summers of our Los Angeles service area or the humidity of our Tennessee home base.
Don't overlook your utility connections. You'll need a dedicated electrical circuit with appropriate amperage (typically 15-30 amps at 208-230 volts), proper drainage for condensate with the right slope, and possibly water supply if you're using water-cooled condensers. And of course, make sure you've handled all the regulatory paperwork—building permits, inspections, and health department requirements won't take care of themselves!
Installation Steps
Installing a walk-in cooler follows a logical sequence that, when done correctly, results in a perfectly functioning unit.
The journey begins with delivery and unloading. Make sure delivery trucks can access your site and have equipment ready for unloading—a forklift or pallet jack will make the job much easier. Before signing that delivery receipt, inspect all components carefully for any shipping damage. It's much easier to address issues immediately than after the delivery team has left.
Panel assembly is where your cooler starts taking shape. If your unit includes floor panels, those go down first, creating the foundation. Then wall panels are erected using cam-lock fasteners that pull the sections tightly together. Ceiling panels cap off the structure, and all joints need proper sealing according to the manufacturer's specifications. Think of it as building a giant insulated puzzle where each piece needs to fit perfectly.
Door installation requires particular attention. The doors are the most frequently used component of your walk-in cooler and proper mounting makes all the difference in energy efficiency. Take time to adjust the hinges for perfect alignment and verify that the door closes completely with an airtight seal. A door that doesn't seal properly is like leaving money on the table—your energy dollars will literally walk right out.
The refrigeration system setup is where technical expertise becomes crucial. The evaporator unit needs mounting inside the cooler, while the condensing unit requires proper positioning according to specifications. Refrigerant lines and drain lines must be connected with the proper pitch for drainage. This is precision work that directly impacts how efficiently your unit will operate.
Finally, electrical connections bring your walk-in cooler to life. Power connections to refrigeration components, wiring of thermostats and controllers, and thorough testing of all electrical systems ensure everything is ready for operation. The system startup and testing phase includes evacuating and charging the refrigeration system, verifying that all components work properly, checking temperature pull-down and stability, and confirming that the defrost cycle operates as designed.
Professional vs. DIY Installation
While some manufacturers market their walk-in coolers as DIY-friendly, there are compelling reasons to consider professional installation.
Professional installation ensures your warranty remains valid—many manufacturers specify that certified technicians must handle certain aspects of installation. Professionals also handle refrigerant properly, which is not just about performance but also legal compliance. Their expertise with electrical and mechanical connections means fewer problems down the road, and they'll typically complete the job faster with fewer errors. Perhaps most importantly, they'll properly test and commission the system, ensuring it's operating at peak efficiency from day one.
If you're considering the DIY route, understand the limitations. This approach typically only works with pre-charged, self-contained units. You'll need basic construction skills and proper tools, and you may still need to hire a professional electrician and HVAC technician for certain aspects. Most importantly, improper installation could void your warranty—a risk that rarely justifies the potential savings.
At American Mortuary Coolers, we take the worry out of installation by providing delivery and professional installation services throughout the contiguous 48 states. Our teams understand the unique requirements of mortuary facilities and ensure that every installation meets both regulatory requirements and our exacting quality standards.
Common Installation Challenges and Solutions
Every installation has its unique challenges, but experience has taught us how to overcome them.
Uneven floors can throw your entire unit out of alignment, but using leveling shims or pouring self-leveling concrete creates the flat surface you need. Limited access to your installation site might seem like a dealbreaker, but modular units with smaller panels can steer tight spaces that would stop larger components in their tracks.
Condensate drainage often presents challenges, especially when gravity drainage isn't possible. In these cases, condensate pumps provide an effective solution. If noise concerns keep you up at night, sound blankets or remote condensing units can significantly reduce operational sound. When your available power doesn't match your walk-in cooler's requirements, you can either upgrade your electrical service or select lower-amperage units designed for efficiency.
Limited headroom doesn't have to be a showstopper either—side-mounted or remote refrigeration systems offer alternatives when vertical space is at a premium.
Proper installation of your walk-in cooler isn't just another box to check—it's an investment in performance that pays dividends for years to come. Taking time to prepare adequately and working with experienced professionals ensures your unit will operate efficiently and reliably throughout its lifespan, whether you're storing flowers, food, or providing essential mortuary services.
Maintenance and Warranty Considerations
Taking care of your walk-in cooler is a bit like maintaining your car – regular attention prevents bigger problems down the road. A well-maintained cooler not only runs more efficiently but can also serve your business faithfully for many more years than a neglected one.
Regular Maintenance Tasks
Your walk-in cooler works hard 24/7, so it deserves some regular TLC. Think of these maintenance tasks as health check-ups for your cooling system.
On a daily or weekly basis, take a quick walk around your cooler. Check those temperature readings to make sure they match what you've set on the thermostat. Give door gaskets a quick inspection – these rubber seals are your first line of defense against cold air escaping. A simple wipe-down of interior surfaces with mild soap and warm water keeps things fresh and prevents odors from developing.
Monthly, dedicate a bit more time to your cooler. Those hinges, door closers, and latches need attention to keep working smoothly. If you have sliding doors, clean those tracks – it's amazing how even a small amount of debris can make them stick. Take a peek at the drain lines too, as clogs can lead to water pooling where you don't want it.
"Regular maintenance checks on your walk-in cooler are key to avoiding costly repairs and ensuring its long-term efficiency," as refrigeration experts often remind us.
Every three months, roll up your sleeves for some deeper maintenance. Those condenser coils collect dust like magnets collect paperclips, so clean them with a soft brush or vacuum. While you're at it, check fan blades for any signs of wear and make sure all electrical connections are snug. This is also a good time for a thorough interior cleaning.
Once a year, it's worth calling in the professionals. They'll check refrigerant levels, test controls, evaluate your compressor, and make sure everything is running at peak efficiency. Think of it as your cooler's annual physical exam.
Importance of Maintenance
Why bother with all this maintenance? The benefits are compelling.
First, you'll dramatically extend your equipment's life. A well-maintained walk-in cooler typically lasts 15-20 years, while neglected units might need replacement after just 8-10 years. That's potentially doubling your investment's lifespan with just a little regular attention.
Your energy bills will thank you too. Clean coils, proper refrigerant levels, and well-sealed doors can slash energy consumption by up to 30%. In today's world of rising energy costs, that's significant savings month after month.
For food service businesses, temperature stability isn't just about efficiency – it's about food safety and quality. Regular maintenance ensures those temperatures stay right where they should be, protecting both your products and your customers.
Then there's the financial perspective. Replacing a failed compressor can cost thousands of dollars, not to mention the potential loss of inventory during downtime. Catching small issues early through regular maintenance is always less expensive than emergency repairs.
Warranty Options
When you invest in a walk-in cooler, the warranty is your safety net. Most manufacturers offer tiered warranty coverage that varies by component.
Panel warranties typically run 10-20 years, covering the structural integrity of your cooler's walls, ceiling, and floor. Door warranties usually range from 1-5 years, protecting against defects in those frequently-used components. Compressor warranties – covering the heart of your cooling system – generally last 1-5 years, while miscellaneous parts usually carry a 1-year warranty.
At American Mortuary Coolers, we understand that our customers rely on consistent, dependable cooling. That's why we stand behind our products with comprehensive warranty coverage across our nationwide service area. Our mortuary-specific walk-in coolers are built for the unique challenges faced by funeral service facilities, with warranty protection that reflects our confidence in their durability.
Tips for Prolonging Lifespan
Want to get the most from your cooling investment? Here are some proven strategies:
Start with proper training. Make sure everyone who uses the cooler understands the basics – from how to minimize door openings to recognizing early warning signs of potential issues.
Keep good records. A simple maintenance log helps track what's been done and when, making it easier to stay on schedule with preventive care.
Address small problems quickly. That slight noise or minor temperature fluctuation? It's trying to tell you something. Responding promptly to these early warning signs can prevent major failures.
Build a relationship with qualified technicians. Having a trusted professional who knows your equipment can make a huge difference when service is needed.
Consider periodic upgrades. As technology improves, replacing older components with more efficient ones can extend your cooler's useful life while reducing operating costs.
One maintenance expert offers this important reminder: "Never lubricate motors that are permanently sealed." This highlights why following manufacturer-specific guidelines is so important – sometimes well-intentioned maintenance can actually cause problems if not done correctly.
With thoughtful maintenance and a solid warranty, your walk-in cooler can be one of the most reliable assets in your business, quietly doing its job year after year while keeping your products at just the right temperature.
Customization Options Available for Walk-In Coolers
When it comes to walk-in coolers, one size definitely doesn't fit all. Today's units offer a wealth of customization options that can transform a standard cooler into the perfect solution for your specific needs. Let's explore how you can tailor your cooler to match your exact requirements.
Exterior Customization Possibilities
The outside of your walk-in cooler makes a statement about your business, and thankfully, there are plenty of ways to make it your own.
Most businesses start with color selection. While standard white remains the most economical and popular choice, many of our customers opt for custom colors that complement their facility or reinforce their brand identity. I recently worked with a funeral home in Nashville that chose a subtle gray exterior to blend seamlessly with their building's architecture.
The finish material is another important consideration. Galvanized steel offers durability at a budget-friendly price point, while aluminum provides a lightweight, corrosion-resistant alternative. For those seeking the ultimate in longevity, stainless steel can't be beaten – though it does come at a premium price. Galvalume, with its aluminum-zinc alloy coating, offers an excellent middle ground for many of our clients.
Many businesses also take advantage of branding opportunities on their walk-in coolers. Custom graphic wraps featuring your logo or integrated signage can transform a utilitarian piece of equipment into a marketing asset. As one satisfied customer told us, "I was able to buy everything I needed in one store," highlighting how convenient it is to work with companies offering comprehensive customization.
Interior Customization
Inside your walk-in cooler is where function truly meets form, with customizations that maximize efficiency and usability.
Shelving systems are perhaps the most important interior element. Adjustable wire shelving promotes maximum airflow around products, while solid shelving works better for containing spills or supporting heavier items. For facilities with changing needs, mobile shelving systems offer unparalleled flexibility. We've seen how the right shelving configuration can dramatically improve workflow and storage capacity.
Lighting makes a huge difference in the usability of your walk-in cooler. Energy-efficient LED lighting has become the standard, providing excellent visibility while keeping energy costs down. Motion-activated systems take efficiency even further by ensuring lights are only on when needed. For businesses displaying products directly to customers, specialized display lighting can improve product appeal – particularly important in floral applications.
Flooring options should match your operational needs. Reinforced flooring supports heavy equipment like loaded carts or pallet jacks, while slip-resistant surfaces improve safety in wet environments. For easy access, integrated ramps eliminate tripping hazards, and diamond tread plates offer exceptional durability in high-traffic areas.
Special Features and Accessories
Modern walk-in coolers can incorporate an impressive array of specialized features that improve functionality and convenience.
Temperature management technology has come a long way. Digital thermometers with remote monitoring capabilities allow you to check temperatures from anywhere, while alarm systems provide peace of mind by alerting you to any temperature excursions. For critical applications, redundant cooling systems ensure your products remain protected even if one system fails. Some of our larger installations even feature multiple temperature zones within a single unit – perfect for businesses with diverse storage needs.
Access and security options have evolved too. Key-coded entry systems restrict access to authorized personnel, while interior safety releases ensure no one ever gets accidentally locked inside. Glass display doors allow for visual merchandising without opening the cooler, and strip curtains help maintain temperature when frequent entry and exit can't be avoided.
Other practical improvements make daily operation smoother. Pressure relief ports eliminate the vacuum effect that can make doors difficult to open. Heated door frames prevent condensation in humid environments. External temperature displays allow for quick verification without opening the door. For specialized storage needs, we can install custom fixtures like meat rail systems.
At American Mortuary Coolers, we understand the unique requirements of funeral service facilities. Our mortuary-specific customizations include specialized body rack systems, reinforced flooring to support the weight of loaded carts, and discreet exterior finishes appropriate for funeral home settings.
Industry-Specific Customizations
Different industries have developed specialized walk-in cooler configurations that address their unique challenges.
Floral businesses typically benefit from higher humidity controls that keep flowers fresh longer, display-oriented shelving and lighting for customer viewing, and glass doors that allow customers to browse without affecting temperature.
Breweries often require substantial floor reinforcement to support heavy kegs and barrels, specialized racking systems for efficient storage, and custom temperature zones for different beer styles at various stages of production.
Restaurant kitchens benefit from pass-through designs that improve workflow efficiency, multiple strategically placed doors for easy access from different work stations, and specialized shelving configured for standard prep containers.
For mortuary facilities – our specialty at American Mortuary Coolers – we focus on reinforced flooring that supports the weight of loaded mortuary carts, specialized rack systems for dignified body storage, superior temperature stability for preservation, and discreet exterior appearances appropriate for funeral service settings.
With our nationwide presence from Johnson City, Tennessee to Los Angeles, California, we've developed customization options that address specific regional needs of mortuary facilities across the country. The humid Southeast requires different considerations than the arid Southwest, and our experience allows us to recommend the most appropriate customizations based on your location, facility size, and operational requirements.
The right customizations transform a standard walk-in cooler into a purpose-built solution that improves efficiency, improves workflow, and perfectly meets your business's unique needs. We'd love to help you explore the possibilities for your facility.
Frequently Asked Questions about Walk-In Coolers
How Do Walk-In Coolers Ensure Food Safety?
Food safety isn't just a legal requirement—it's a fundamental responsibility for any food-related business. Walk-in coolers are your frontline defense in this critical battle against foodborne illness.
At their core, these units maintain the consistent cold temperatures needed to keep bacteria at bay. Most food safety experts recommend keeping your walk-in cooler between 35°F and 38°F—that sweet spot where food stays fresh but bacteria growth slows to a crawl.
"It's all about staying out of the danger zone," explains one food safety consultant. "When temperatures rise above 40°F, bacteria can double in number every 20 minutes. Your walk-in cooler is essentially putting those microbes into hibernation."
Modern units come equipped with precise digital controls that maintain temperatures within a single degree of your setting. This consistency is crucial—even brief temperature spikes can accelerate spoilage and compromise safety. Many of today's systems also include alarm features that alert you if temperatures drift beyond safe ranges, giving you peace of mind even when you're not on-site.
Beyond temperature control, walk-in coolers support proper storage practices that prevent cross-contamination. With adequate shelving and space, you can implement proper food storage hierarchies—keeping raw meats below ready-to-eat items, for instance—that further improve safety.
For businesses subject to health department inspections, your walk-in cooler plays a starring role in regulatory compliance. Many modern units offer temperature logging capabilities that provide documentation for HACCP protocols and health department requirements. This record-keeping can be invaluable during inspections and for your own quality assurance programs.
What Are Common Materials and Insulation Types Used in Walk-In Coolers?
The materials that make up your walk-in cooler might not be the most exciting topic, but they're absolutely crucial to its performance and longevity. Let's break down what goes into these essential units.
The outer and inner "skins" of most walk-in coolers are typically metal, with several options available. Galvanized steel offers a good balance of durability and cost-effectiveness, making it the most common choice. For environments where corrosion resistance is paramount, stainless steel provides superior protection—though at a higher price point. Aluminum offers natural corrosion resistance with lighter weight, while Galvalume (steel coated with an aluminum-zinc alloy) provides improved durability for outdoor installations.
Between these metal skins lies the heart of your cooler's efficiency: the insulation. Most quality walk-in coolers use polyurethane foam insulation, which offers the highest R-value per inch of any commonly used material. This means more effective temperature control and lower energy bills. The industry standard is a 4-inch thickness, providing the R-25 value required by energy codes for coolers (freezers require R-32).
"The way the insulation is installed makes all the difference," notes one industry veteran. "Foamed-in-place technology creates a seamless barrier without the thermal bridges that can compromise efficiency."
Floor materials deserve special attention since they bear the weight of everything inside. Options range from standard aluminum tread plate to stainless steel for high-sanitation environments. For heavy-duty applications where pallet jacks or carts will be used regularly, reinforced flooring is essential. Many facilities also opt for anti-slip coatings to improve workplace safety.
The joints where panels connect are another critical consideration. Quality walk-in coolers use cam-lock systems with gaskets that create tight seals, maintaining the thermal envelope and preventing moisture infiltration that could degrade insulation over time.
At American Mortuary Coolers, we understand that mortuary applications have unique material requirements. Our units feature materials specifically selected for their ability to maintain the cleanliness, temperature stability, and durability that funeral service professionals demand.
What Are the Key Factors in Choosing a Walk-In Cooler?
Selecting the right walk-in cooler for your business isn't a decision to take lightly. This equipment represents a significant investment that will impact your operations for years to come. Let's explore the most important considerations that should guide your choice.
First and foremost, accurately assessing your space requirements is crucial. One helpful rule of thumb: one cubic foot of cooler space can store approximately 28 pounds of food. But don't just calculate for today's needs—consider where your business might be in five years. Will you need more capacity? Is expansion a possibility? The standard interior height for most walk-in coolers is 7'6", but custom heights are available if your space has specific constraints.
Budget considerations naturally play a major role in the decision process. Small, basic models start around $4,625, but this is just the beginning of your investment. Be sure to factor in installation costs, including site preparation and electrical work. More importantly, look beyond the initial price tag to consider long-term operating costs. A slightly more expensive unit with better insulation and more efficient components can pay for itself many times over through reduced energy bills.
"I made the mistake of buying the cheapest option," confesses one restaurant owner. "Within three years, I'd spent more on energy and repairs than I would have if I'd just bought the better unit to begin with."
Energy efficiency deserves special attention when evaluating different models. Higher R-value insulation, self-closing doors, and modern refrigeration components with EC motors can significantly reduce your monthly operating costs. Look for ENERGY STAR certified units when available, as these meet strict efficiency guidelines that can translate to substantial savings.
Your specific operational needs should heavily influence your selection. Consider your workflow—where will the unit be located relative to your preparation areas? How frequently will staff need to access it? Door placement and interior layout should support efficient operations rather than creating bottlenecks. Some businesses benefit from glass display doors, while others need reinforced flooring for heavy equipment.
"I had a limited space and needed a cooler that would fit," shares one customer in a testimonial. "I called and they had a box custom made for me cheaper than other stores were charging me for much smaller boxes."
At American Mortuary Coolers, we understand that funeral service facilities have unique requirements. Our nationwide experience—from our home base in Tennessee to serving clients in California, Illinois, and beyond—has taught us that listening carefully to our customers' specific needs is the first step in providing the perfect walk-in cooler solution. We take pride in creating custom units that precisely match the operational, spatial, and aesthetic requirements of modern mortuary facilities.
Conclusion
A walk-in cooler represents a significant investment for any business that relies on temperature-controlled storage. Throughout this guide, we've explored the essential components, features, and considerations that should inform your purchase decision.
Key Takeaways
When it comes to walk-in coolers, understanding what matters most can make all the difference between a smart investment and a costly mistake. The insulated panels, refrigeration systems, and door assemblies all work together like a well-rehearsed orchestra to maintain those critical temperatures your products need.
Choosing the right size is a bit like finding the perfect pair of shoes - too small and you'll be cramped and uncomfortable, too large and you're wasting resources. By carefully considering your peak storage needs, you can find that "just right" solution that keeps everything running efficiently.
The indoor versus outdoor debate really comes down to your specific situation. Indoor units offer protection from the elements and easy access, while outdoor models free up valuable interior space. It's not unlike deciding between a basement or detached garage - each has its place depending on your needs and constraints.
Today's walk-in coolers have come a long way in energy efficiency. With high-R-value insulation, smart controllers, and efficient motors, modern units can significantly reduce your operating costs while still keeping everything perfectly chilled. Think of it as the difference between an old gas-guzzler and a modern hybrid - same destination, much less expense getting there.
Proper installation isn't just a recommendation; it's essential for getting the performance you're paying for. Like building a house, the foundation matters, and cutting corners during installation can lead to years of problems down the road. That's why professional installation is usually worth every penny.
Maintenance might seem like a chore, but it's truly the secret to longevity. Regular check-ups and cleaning keep your walk-in cooler running at peak efficiency while preventing those midnight emergency repair calls that always seem to come at the worst possible time.
One of the most exciting aspects of modern walk-in coolers is the ability to customize them to your exact needs. From specialized shelving to custom dimensions, today's units can be custom to fit your space and workflow perfectly.
"A walk-in cooler can be one of the largest upgrade purchases your business makes," as we noted at the beginning of this guide. This statement underscores the importance of making an informed decision based on thorough research and consideration of your specific requirements.
The American Mortuary Coolers Advantage
At American Mortuary Coolers, we specialize in crafting custom mortuary coolers and related equipment for the funeral industry. Our expertise extends to all types of walk-in coolers, with a particular focus on the unique requirements of mortuary facilities.
What makes us different isn't just what we build, but how we approach each project. We believe in listening first and building second. Every facility has unique needs, and we take pride in finding the perfect solution for each client.
Our nationwide service network means you're never far from help when you need it. From our home base in Tennessee to service points across the country—Johnson City to Los Angeles and everywhere in between—we provide direct delivery and service to the contiguous 48 states. When you need us, we're there.
We understand that standard solutions often fall short in specialized environments like mortuary services. That's why we focus on custom solutions that address your specific challenges rather than trying to make a one-size-fits-all product work in your unique setting.
Our walk-in coolers are built with durability as a core principle. We select materials and construction techniques that ensure long-term reliability even under demanding conditions. After all, when you're providing essential services, equipment failure simply isn't an option.
Whether you're running a restaurant, grocery store, floral shop, brewery, or mortuary facility, your walk-in cooler isn't just another piece of equipment—it's the backbone of your operation. It protects your inventory, ensures product quality, and helps you meet regulatory requirements day in and day out.
We invite you to explore how American Mortuary Coolers can help you find the perfect walk-in cooler solution for your business needs. Our team of experts is ready to guide you through the selection process, ensuring you receive a system that provides optimal performance, energy efficiency, and value.
For more information or to discuss your specific requirements, please contact us today. Let us help you keep your cool with a solution perfectly custom to your needs.