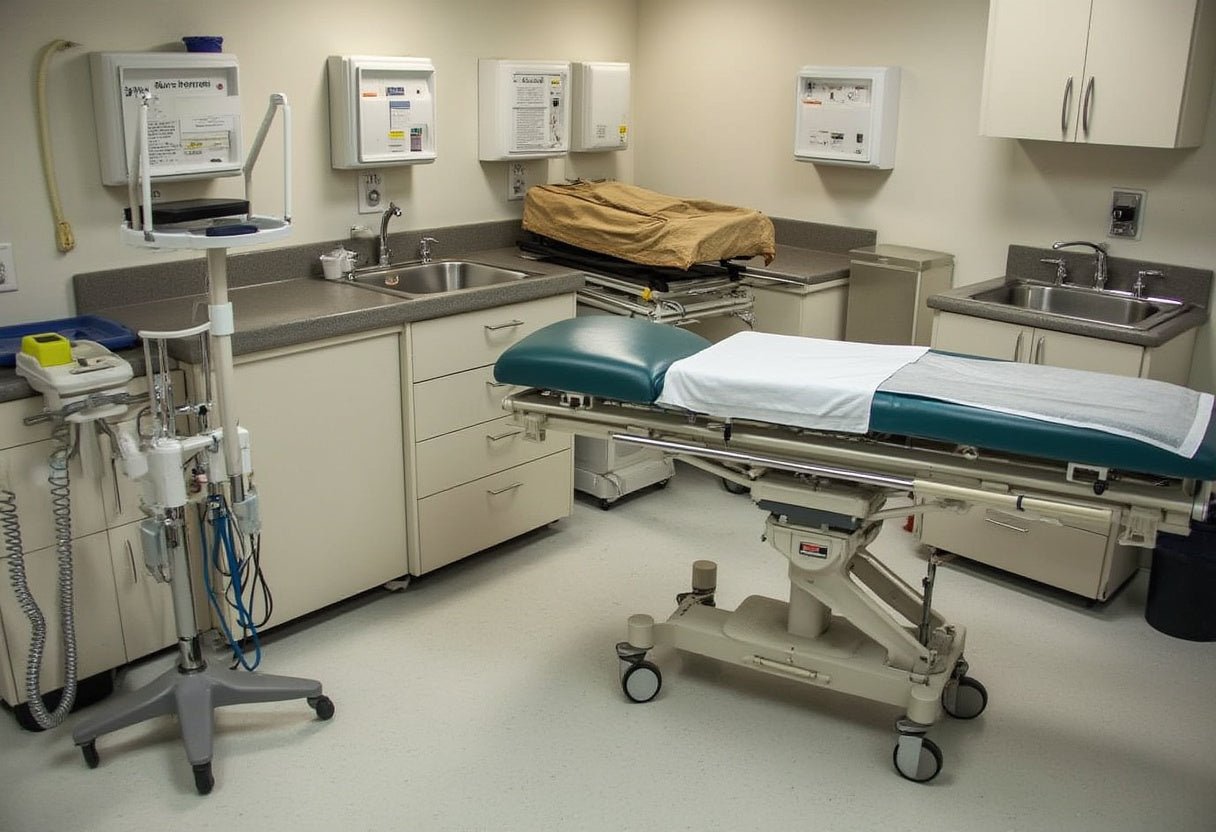
The Definitive Guide to Quality Professional Mortuary Equipment
The Evolving World of Professional Mortuary Equipment
Professional mortuary equipment encompasses the specialized tools, devices, and systems designed for funeral homes, mortuaries, and pathology labs. This equipment plays a crucial role in facilitating dignified end-of-life services while ensuring safety and efficiency.
Essential Professional Mortuary Equipment:
- Embalming Tables & Stations: Stainless steel surfaces with drainage systems
- Refrigeration Units: Walk-in coolers, drawer systems, and portable units
- Body Lifts & Transporters: Hydraulic or battery-powered systems (500-1000 lb capacity)
- Autopsy Tables & Instruments: Specialized for forensic and pathological examinations
- Preparation Room Supplies: Disinfectants, instruments, and ventilation systems
Since 1970, the mortuary equipment industry has evolved significantly, with manufacturers now emphasizing durability, customization, and innovative features. Modern equipment incorporates advanced materials like industrial-grade stainless steel (304 grade), ergonomic designs, and electronic systems for improved safety and efficiency.
The quality of mortuary equipment directly impacts not only operational efficiency but also the dignity with which the deceased are treated. Equipment failure or inadequate systems can compromise both staff safety and the quality of services provided to grieving families.
I'm Mortuary Cooler, a national-level mortuary cooler supplier with experience in the professional mortuary equipment industry. My work involves helping funeral directors select appropriate refrigeration solutions that meet both regulatory requirements and practical needs of funeral establishments.
Key Professional mortuary equipment vocabulary:
Essential Types of Professional Mortuary Equipment
The funeral industry relies on specialized equipment to provide dignified care for the deceased while ensuring safety and efficiency for staff. At American Mortuary Coolers, we've observed that well-equipped facilities can significantly improve service quality while reducing operational challenges. Here's a comprehensive overview of the essential professional mortuary equipment that forms the backbone of modern funeral services.
Embalming Tables and Stations
Embalming tables represent the centerpiece of any preparation room. These specialized workstations are designed to facilitate the embalming process with maximum efficiency and sanitation.
Modern embalming tables typically feature 304-grade stainless steel construction for durability and ease of cleaning. The integrated drainage systems with proper sloping channel fluids away efficiently, while height-adjustable mechanisms (hydraulic or electric) create ergonomic working conditions for embalmers of all heights.
The best tables include reinforced welding to support weights of 600+ pounds, which has become increasingly important in recent years. Removable headrests allow easier access during preparation, and spill-containing edges prevent contamination of the surrounding area – a small detail that makes a big difference in daily operations.
"Choosing the right embalming table goes beyond just how it works; it's about respecting the dignity of the people you help while ensuring staff can work efficiently in sometimes challenging conditions," notes a veteran funeral director with over 30 years of experience.
The latest innovations include tables with built-in ventilation systems to reduce exposure to chemicals and customizable features like adjustable angle positioning. Some premium models now incorporate warming systems to assist with arterial embalming in colder environments – a thoughtful touch that shows how far this equipment has evolved.
Mortuary Refrigeration Units
Refrigeration units are perhaps the most critical pieces of professional mortuary equipment, as they ensure the preservation of the deceased prior to preparation or viewing. At American Mortuary Coolers, we specialize in these essential systems, which come in several configurations.
Walk-in mortuary coolers provide large-capacity storage that can accommodate multiple bodies, making them ideal for busier funeral homes or during disaster response situations. For those with space constraints, drawer refrigeration systems offer a more compact solution, keeping each body in a separate, easily accessible drawer.
When flexibility is needed, portable refrigeration units serve smaller facilities or provide temporary additional capacity during busy periods. For facilities with diverse preservation needs, combination cooler-freezer units offer versatility with both refrigeration and freezing capabilities in a single system.
Quality refrigeration units maintain temperature control precision (typically 35-40°F/2-4°C) with minimal fluctuation. They also feature humidity management capabilities to prevent dehydration of the deceased, an often overlooked but crucial aspect of preservation. Backup power systems ensure uninterrupted operation during outages – because we understand that power failures don't respect business hours.
Our American Mortuary Coolers are designed with redundant cooling systems to prevent failures and include remote temperature monitoring capabilities, giving funeral directors peace of mind even when they're away from the facility.
More info about mortuary refrigeration units
Body Lifts and Transport Equipment
Safe and dignified transport of the deceased requires specialized equipment designed to minimize physical strain on staff while maintaining respectful handling.
Mortuary cots with adjustable height features have transformed how removal teams work, reducing back injuries and making transfers smoother. Hydraulic body lifts assist with transferring the deceased between surfaces, while the newer battery-powered lifts can handle weights up to 1000 pounds with minimal physical effort – a game-changer for smaller funeral homes with limited staff.
Simple tools like transfer boards and sliders facilitate moving the deceased with reduced strain, proving that sometimes the most helpful innovations aren't the most complex. For more public-facing situations, church trucks/biers provide decorative rolling carts used during visitations and services, combining functionality with appropriate aesthetics.
Link, a leader in manufacturing mortuary deck systems for over 20 years, emphasizes that "leading with humility by putting safety first" is essential when designing transport equipment. Their approach focuses on improving daily operations for funeral directors through purpose-built products.
For bariatric cases, specialized equipment with improved weight capacities (often 900+ pounds) ensures safe handling without compromising dignity. Features like break-apart designs and quick-release mechanisms make these tools practical for various operational scenarios, allowing funeral professionals to provide the same level of care to everyone regardless of size.
Autopsy Tables and Instruments
While primarily used in medical examiner facilities and hospital pathology departments, some funeral homes with preparation rooms may also use autopsy equipment for specialized cases.
Autopsy tables typically feature downdraft ventilation to protect staff from airborne pathogens and chemicals. They include improved drainage systems and specialized washing features that maintain a clean working environment. The best modern tables incorporate height adjustability (32-38 inch range), integrated scale systems for weight documentation, and specialized lighting to improve visibility during procedures.
The toolkit for these procedures includes precision dissection instruments like scalpels, scissors, and forceps, all designed for specific forensic applications. Specimen storage solutions ensure proper preservation of tissue samples when needed for further testing.
Proper documentation equipment, including specialized cameras and measurement tools, helps create accurate records. Equally important are the protective barriers and ventilation systems that ensure staff safety during procedures – because protecting the living while caring for the deceased is always the priority.
For funeral homes that occasionally handle forensic cases, modular systems that can convert between embalming and autopsy functions offer practical versatility without requiring separate dedicated equipment. This adaptability allows smaller facilities to expand their service offerings without doubling their equipment investments.
The Importance of Quality and Durability in Mortuary Equipment
When it comes to professional mortuary equipment, quality and durability aren't just nice-to-have features—they're absolute necessities. As we've learned from our years at American Mortuary Coolers, the equipment funeral professionals use directly impacts their daily operations, staff wellbeing, and most importantly, the dignity they can provide to families during difficult times.
Material Considerations for Longevity
The materials used in mortuary equipment tell the real story about how long that equipment will serve your facility. We've seen how the right materials make all the difference.
304-grade stainless steel stands as the gold standard in our industry, and for good reason. This industrial-grade material laughs in the face of the harsh chemicals used in embalming and cleaning processes. While cheaper alternatives might look similar on day one, they begin to pit, corrode, and deteriorate after months of chemical exposure—not exactly what you want in equipment that represents your professional standards.
For structural components, zinc-treated steel creates frameworks that remain rock-solid year after year. One of our customers recently told us, "The cooler we bought from you guys 15 years ago looks almost identical to the day it was installed." That's the power of starting with the right materials.
Components that contact deceased individuals often use medical-grade PVC because it prevents scratching during transfers and stands up to thousands of cleaning cycles without breaking down. And those professional powder and epoxy coatings aren't just for looks—they create a barrier that prevents chipping and peeling, keeping equipment looking professional even after years of daily use.
As one equipment manufacturer with over 55 years in the industry once told me, "We've seen facilities still using our tables after 25+ years of daily use—that's the difference quality materials make." I couldn't agree more.
Impact on Operational Efficiency
The quality of your mortuary equipment affects your daily operations in ways that might surprise you. When we talk with funeral directors who've upgraded from budget equipment to quality pieces, we hear the same feedback time and again.
Reduced downtime tops the list of benefits. Quality equipment simply breaks down less often, which means you're not scrambling to find alternatives or apologizing to families for delays. The peace of mind that comes from knowing your equipment won't fail during a procedure is impossible to overstate.
Quality equipment is also designed with ease of operation in mind. Handles are placed where they make ergonomic sense. Controls are intuitive. Movements are smooth. These seemingly small details add up to significantly reduced staff fatigue at the end of a long day.
A funeral director friend in the Midwest shared something that stuck with me: "After upgrading to a premium hydraulic embalming table, we reduced our preparation time by nearly 20% and significantly decreased staff complaints about back strain." That efficiency translates directly to better service and healthier staff.
Even maintenance becomes less of a headache. Quality equipment typically features accessible components that make routine maintenance straightforward rather than a puzzle. And when needs change, durable equipment often adapts with you, accommodating modifications or upgrades without requiring complete replacement.
Safety Considerations
Let's talk about safety, because this is where cutting corners can have serious consequences. Quality equipment maintains its structural integrity throughout its entire lifespan, consistently supporting its rated load capacity without developing weak points.
The smooth operation of well-engineered mechanisms eliminates jerky movements that could cause injuries to staff or damage to the deceased. Reliable locking mechanisms prevent unexpected movement during procedures—a critical safety feature that budget equipment often sacrifices.
For equipment used in wet environments (which describes most mortuary equipment), proper electrical insulation is non-negotiable. Quality manufacturers understand this and design accordingly, while lower-quality alternatives might take shortcuts that create hazards.
Industry data backs this up: facilities investing in premium equipment consistently report fewer workplace injuries and workers' compensation claims related to equipment failures. When you consider the cost of even one workplace injury, quality equipment starts looking less like an expense and more like insurance.
Material Science Behind Quality Equipment
The science behind truly durable mortuary equipment goes beyond just selecting good materials—it's about how those materials come together.
Seamless welding techniques eliminate crevices where biological materials could accumulate, making sanitization more effective and preventing cross-contamination. Precision machining ensures components fit together properly, reducing wear from parts rubbing or grinding against each other.
Quality manufacturers like us at American Mortuary Coolers use strategic reinforcement to strengthen high-stress areas without adding unnecessary weight that would make equipment harder to move. And those seemingly minor corrosion-resistant fasteners? They prevent the weak points that often develop around bolts and screws in lesser equipment.
Scientific research on equipment safety standards
Companies like CEABIS, a leader in the funeral sector since 1970, demonstrate through their continuous investment in product quality that materials and construction methods directly influence not just equipment longevity but also functionality throughout its service life.
At American Mortuary Coolers, we've built our reputation on understanding these principles. We know that when you invest in quality equipment, you're not just buying a product—you're investing in your facility's efficiency, your staff's wellbeing, and ultimately, in the level of care you can provide to the families who depend on you.
Latest Innovations in Mortuary Equipment Technology
The world of professional mortuary equipment is experiencing a remarkable change. Gone are the days of purely mechanical systems and basic functionality. Today's funeral industry professionals have access to sophisticated technology that improves every aspect of their important work.
Innovations in Professional Mortuary Equipment
The refrigeration systems we create at American Mortuary Coolers now feature smart technology that would have seemed like science fiction just a decade ago. Our newest models include remote temperature monitoring that sends alerts directly to your smartphone if conditions change unexpectedly. This provides peace of mind, especially during weekends or holidays when staff may be limited.
Energy efficiency has become a priority in modern equipment design. The variable-speed compressors in our cooling systems adjust their output based on actual conditions, rather than running at full capacity constantly. This not only reduces utility costs but also extends equipment life significantly.
"I used to worry constantly about our cooler during hot summer weekends," shares a funeral director from Memphis. "Now I can check temperatures from my phone while at my son's baseball game. It's been a game-changer for my peace of mind."
Body handling has become safer and more dignified thanks to technological advances. The latest battery-powered hydraulic lifts can handle weights up to 1000 pounds with minimal physical effort. This means that even smaller funeral homes can manage bariatric cases without risking staff injuries or compromising dignity.
The ergonomic improvements in transport equipment are just as important as the power upgrades. Precision control mechanisms allow for smooth, gentle transfers, while thoughtfully designed handles reduce operator fatigue during busy periods. Some systems now even include collision avoidance features that prevent accidental contact with doorframes or walls.
Material science has revolutionized the surfaces that come into contact with both the deceased and preparation chemicals. Many new preparation tables feature antimicrobial surface treatments that inhibit bacterial growth between cleanings. This additional layer of protection helps maintain proper sanitation even during the busiest times.
The one-piece seamless tops on modern embalming tables eliminate the crevices where fluids and tissue could previously accumulate. This design improvement not only makes cleaning easier but significantly reduces the risk of cross-contamination. The improved drainage systems in these tables direct fluids more efficiently, making the preparation process cleaner and more controlled.
Digital integration is perhaps the most visible change in new mortuary equipment. RFID tracking systems help maintain proper identification and chain of custody throughout the care process. Digital documentation interfaces allow for paperless record-keeping, reducing both administrative burden and the chance for errors.
Some advanced preparation tables now include integrated scale systems that automatically record weight data – information that's critical for proper chemical calculations and documentation. This integration eliminates the need for separate weighing steps and reduces the chance of transcription errors.
Sustainability has become a driving force in equipment design as funeral professionals increasingly consider their environmental impact. Water recirculation systems dramatically reduce consumption during preparation procedures, while energy recovery ventilation improves air quality while minimizing heating and cooling costs.
At American Mortuary Coolers, we've acceptd solar backup power systems for critical refrigeration units, ensuring continuous operation even during power outages. This technology provides both environmental benefits and practical security during emergencies.
The quieter operation of modern equipment might seem like a small improvement, but it creates a more respectful environment for both the deceased and the professionals caring for them. Sound-dampening technologies have reduced the mechanical noise that once filled preparation rooms, creating a more dignified atmosphere.
Modular design approaches allow funeral homes to customize their equipment to their specific needs and space constraints. Rather than one-size-fits-all solutions, today's professional mortuary equipment can be configured to work efficiently in facilities of any size.
These technological advances aren't just about efficiency – they reflect the funeral industry's ongoing commitment to excellence and dignity in end-of-life care. As we continue developing new solutions at American Mortuary Coolers, we remain focused on innovations that truly serve the needs of funeral professionals and the families they help during difficult times.
Key Considerations When Selecting Mortuary Refrigeration Units
Choosing the right refrigeration unit is one of the most important decisions a funeral home will make. At American Mortuary Coolers, we've helped hundreds of funeral professionals steer this critical choice, and we understand that refrigeration systems are truly the backbone of professional mortuary equipment.
Capacity Planning and Space Utilization
When thinking about capacity, you need to look beyond just your average case count. We always tell our clients to examine their seasonal patterns too. Many funeral homes experience significant volume fluctuations throughout the year, and being caught without enough refrigeration during a busy period can create serious challenges.
"We recommend facilities plan for at least 150% of their current average capacity needs," says our lead designer at American Mortuary Coolers. "This provides flexibility during unexpected surges and accommodates future growth."
Space constraints are a common concern, especially in older facilities. That's why we design custom solutions that maximize capacity within your existing footprint. Our drawer systems use vertical space much more efficiently than traditional shelving, and our specialized corner units can transform otherwise unusable areas into functional storage. One funeral director in Ohio told us, "I never thought we could fit eight positions in that space, but your team made it happen."
Temperature Control and Monitoring Systems
Maintaining the right temperature isn't just about having a good cooling system—it's about precision and reliability. Standard units should maintain 35-40°F (2-4°C), but the best systems offer more than just basic cooling.
Temperature uniformity is crucial—you want consistent conditions throughout the unit with no hot or cold spots. The recovery rate also matters tremendously. This measures how quickly your system returns to the set temperature after door openings, which happen frequently in busy establishments.
Our American Mortuary Coolers feature dual compressor systems in larger units, ensuring continued operation even if one compressor requires service. We've also invested heavily in remote monitoring technology that lets you check conditions from anywhere via smartphone. One funeral director told us, "Getting temperature alerts on my phone gives me peace of mind when I'm away from the funeral home."
Energy Efficiency Considerations
The truth about refrigeration units is that operating costs over the equipment's lifespan often exceed the initial purchase price. That's why energy efficiency should be a top consideration.
High-quality insulation with superior R-values dramatically reduces energy consumption. The compressor efficiency ratings (look for high SEER/EER numbers) tell you how efficiently the unit converts electricity into cooling power. Even seemingly small details like door seal design make a huge difference—our magnetic seals and double gaskets minimize cold air loss during access.
"One funeral home in the Northeast Region reported a 37% reduction in electricity costs after upgrading to our energy-efficient cooling systems," notes our technical director. "The investment paid for itself in under three years through reduced utility bills."
LED lighting systems inside units serve a dual purpose—they reduce both energy consumption and heat generation. And our smart defrost systems operate only when needed, rather than on a fixed schedule, further reducing energy waste.
Compliance and Regulatory Requirements
Refrigeration units must meet various standards, and navigating these requirements can feel overwhelming. Local health departments often specify minimum cooling capacity and temperature requirements, while OSHA has its own standards regarding worker safety features.
Accessibility matters too—units should be designed for staff with various physical capabilities. Electrical code compliance ensures your equipment operates safely, and environmental regulations (particularly regarding refrigerant types) continue to evolve.
At American Mortuary Coolers, we stay current with regulatory requirements across all 50 states, ensuring our equipment meets or exceeds applicable standards. We also provide comprehensive documentation to make inspections and certifications as smooth as possible.
Installation and Integration Considerations
The physical installation process deserves careful thought before you purchase. We've seen many situations where funeral homes selected equipment without considering delivery access—only to find their new unit wouldn't fit through doorways or steer tight hallway turns.
Floor load capacity is especially relevant for multi-body walk-in units, which can be surprisingly heavy when fully loaded. Electrical requirements must be evaluated in advance—adequate power supply and circuit capacity are essential for proper operation.
Proper ventilation around condensers and compressors isn't just about performance—it affects equipment lifespan too. And integration with existing systems, including backup generators, should be planned carefully.
Our team conducts thorough site surveys before finalizing designs, ensuring all installation challenges are addressed before equipment is manufactured. We offer complete installation services in all regions we serve, including the Southeast, Southwest, Midwest, Northeast, Rocky Mountain, and Pacific regions.
"The installation team was incredible," shared a funeral director from Georgia. "They worked around our schedule, minimized disruption to our services, and left everything spotless when they finished. That level of professionalism matters when you're running a funeral home."
More info about mortuary coolers
Compliance with Health and Safety Regulations
Adherence to health and safety regulations is non-negotiable when it comes to professional mortuary equipment. These standards protect both staff and the public while ensuring the dignified treatment of the deceased.
Understanding Regulatory Frameworks
The world of mortuary regulations can feel like navigating a maze sometimes. Several different agencies have their say in how things should be done, and keeping up with all of them takes real dedication.
OSHA sets the foundation for workplace safety standards, covering everything from how to handle bloodborne pathogens to chemical exposure limits and equipment safety requirements. Meanwhile, the EPA keeps a watchful eye on how chemicals are disposed of, monitors air quality, and regulates wastewater management.
Your state's Funeral Board likely has specific requirements for preparation rooms and equipment too. And don't forget local Health Departments, which often have the final word on refrigeration requirements and sanitation standards. The CDC rounds out this regulatory family with guidelines for infection control, which became especially important during recent years.
"Navigating this complex web of regulations can be challenging," as our compliance specialist at American Mortuary Coolers often says. "That's why we design our equipment to meet or exceed requirements across all jurisdictions, making compliance simpler for our clients."
Key Compliance Areas for Mortuary Equipment
Bloodborne Pathogen Standards
OSHA's Bloodborne Pathogens Standard has dramatically shaped how we design mortuary equipment. Modern embalming tables aren't just about functionality – they're carefully crafted with non-porous surfaces that prevent absorption of potentially infectious materials.
Good equipment design prioritizes cleanability, with smooth surfaces and minimal seams where contaminants could hide. Our embalming stations at American Mortuary Coolers feature seamless construction with raised edges specifically designed to contain fluids and prevent cross-contamination – something that makes both cleaning easier and inspections less stressful.
The standard also requires proper sharps management and features that minimize splashing during procedures. These aren't just regulatory checkboxes; they're essential protections for the professionals who use this equipment every day.
Chemical Safety Compliance
Working with preservation chemicals brings its own set of challenges and regulatory requirements. Quality equipment needs to integrate with proper ventilation systems – something the National Funeral Directors Association takes seriously, recommending preparation rooms maintain 12 air changes per hour.
Materials used in construction must be chemical-resistant, able to withstand repeated exposure to formaldehyde and other preservation chemicals without degrading. Proper fluid management systems aren't just about cleanliness; they're essential for preventing chemical exposure that could harm staff.
Many funeral homes are also incorporating emergency features like eyewash stations directly integrated with preparation equipment – a small addition that can make a huge difference in an emergency.
Ergonomic and Mechanical Safety
The physical demands of funeral work can take a toll on staff. That's why modern equipment increasingly features lift assist mechanisms – hydraulic or electric systems that reduce the need for manual lifting.
"Our hydraulic and battery-powered lift systems are tested to 150% of their rated capacity," our engineering director often points out with pride. "This exceeds the industry standard testing protocol of 125% and gives our customers peace of mind."
Other important safety features include guards that prevent accidental injury during operation, stability features that prevent tipping, and clear markings indicating maximum safe working loads. These aren't luxuries – they're necessities for preventing the back injuries and strains that are all too common in this profession.
Electrical Safety
Water and electricity make nervous neighbors, especially in preparation rooms where cleaning is frequent and thorough. Equipment with electrical components requires special attention to safety, starting with ground fault protection and waterproof connections.
Proper grounding ensures equipment doesn't become energized, while appropriate circuit protection prevents overloads and electrical fires. At American Mortuary Coolers, all our refrigeration systems undergo rigorous electrical safety testing and certification before they leave our facility – because we understand that reliability isn't just about convenience, it's about safety.
Documentation and Training Requirements
Compliance extends beyond the physical equipment to include proper documentation and training. Operating manuals need to provide clear instructions for safe operation. Maintenance records should document regular service and repairs. Staff need access to comprehensive training materials.
We provide complete documentation packages with all our equipment, including recommended cleaning protocols, maintenance schedules, and staff training guides. These materials aren't just about checking regulatory boxes – they're about empowering funeral professionals to work safely and efficiently.
Emerging Regulatory Trends
The regulatory landscape never stands still. We're seeing increasing focus on energy efficiency standards for refrigeration equipment, with states adopting stricter requirements for performance and efficiency. There's also growing emphasis on sustainable materials and environmentally responsible manufacturing practices.
Digital compliance tracking is becoming more common, with electronic systems for documenting regulatory adherence replacing paper records. And perhaps most significantly, there's been renewed attention to improved infection control protocols, particularly following lessons learned during the COVID-19 pandemic.
At American Mortuary Coolers, we actively monitor these regulatory developments across all regions we serve. This vigilance ensures our equipment remains compliant with both current requirements and those on the horizon – giving our customers one less thing to worry about in their daily operations.
Customization in the Design and Manufacturing of Mortuary Equipment
When it comes to professional mortuary equipment, one size definitely doesn't fit all. Every funeral home, hospital morgue, and medical examiner's office has unique needs that standard, off-the-shelf equipment simply can't address. That's where customization becomes not just valuable, but essential.
Understanding the Customization Process
Here at American Mortuary Coolers, we've refined our customization journey to ensure your equipment fits your facility perfectly—both physically and operationally. It starts with a conversation. We take time to understand not just what you need, but why you need it.
Our design director puts it best: "The most successful customization projects begin with a thorough understanding of not just the physical space, but how the team works within it. We observe workflows and identify pain points before proposing solutions."
The process unfolds naturally from there. We'll assess your space (either in person or virtually), draft preliminary designs that address your specific challenges, and collaborate with you to refine them. Once you're completely satisfied, we move to precision manufacturing, rigorous quality testing, and professional installation.
Common Customization Areas
Size and Dimensional Modifications
Sometimes, the standard dimensions just won't work with your space. Maybe you're dealing with narrow doorways, limited floor space, or unusual ceiling heights. We understand these challenges because we've solved them before.
Take our client in Chicago. They had a preparation room with an immovable structural column right in the middle—a real headache for standard equipment. We designed a split-level refrigeration unit that worked around this obstacle while still providing all the capacity they needed. Problem solved!
Functional Adaptations
Beyond just fitting physically, your equipment needs to support your unique operational workflow. We've created specialized access configurations for unusual room layouts and upgraded cooling systems for facilities in scorching climates like Arizona and Texas.
A funeral director from Dallas shared: "Our mortuary handles a high volume of bariatric cases. American Mortuary Coolers designed a specialized system with reinforced trays and wider spacing that has transformed our ability to manage these cases with dignity."
Other functional customizations we've provided include hybrid refrigeration/freezer units with independent temperature zones and custom integration with existing building management systems. Whatever your operational challenge, we've probably seen it—and solved it—before.
Aesthetic Customizations
While function comes first in professional mortuary equipment, appearance matters too, especially in facilities where families might see the equipment. Beyond our standard stainless steel, we offer various exterior finishes that can complement your facility's décor.
One memorial center on the West Coast requested refrigeration units with wood-grain exterior finishes to blend seamlessly with their contemporary viewing rooms. This created a more homelike environment for families choosing to view their loved ones before final disposition.
We can also incorporate custom lighting, viewing-friendly designs for facilities that encourage family participation, and elements that accommodate specific cultural or religious practices. Your equipment should support your mission and values, not just your operational needs.
Material and Component Selection
Different environments create different demands on materials. Coastal locations deal with salt air that can accelerate corrosion. Some facilities prioritize antimicrobial surfaces for additional protection. Others need specialized insulation for extreme climates or noise-sensitive locations.
We can customize the very building blocks of your equipment to ensure longevity and performance in your specific environment. This might mean alternative refrigerants for environmentally-conscious facilities or specialized backup system integration for areas prone to power outages.
The Economics of Customization
I won't sugarcoat it—custom equipment typically costs more upfront than standard models. But our clients consistently find that the long-term benefits justify the investment.
A funeral director from Pittsburgh told us: "The additional investment in our custom refrigeration system paid for itself within 18 months through reduced labor costs and improved energy efficiency."
Custom equipment creates value through improved operational efficiency (equipment custom to your specific workflows saves time), extended equipment lifespan (purpose-built solutions typically outlast adapted standard equipment), and improved staff satisfaction (less frustration from working with ill-fitting equipment).
Plus, you'll maximize functionality from your available square footage—crucial for urban facilities where space comes at a premium—and future-proof your operation with designs that can accommodate anticipated changes in case volume or types.
As CEABIS, a respected industry voice, says: "The approach of continuously improving daily operations for funeral directors and livery operators through purpose-built products" isn't just a nice idea—it's essential for operational excellence.
At American Mortuary Coolers, we don't just build equipment; we build solutions that make your work easier, more efficient, and more dignified. Because in this profession, the details matter—and so does having equipment that works with you, not against you.
Financing Options for Purchasing Mortuary Equipment
Let's face it - quality professional mortuary equipment represents a significant investment for any funeral establishment. Whether you're opening a new facility or upgrading your existing equipment, understanding your financing options can make all the difference in making smart business decisions that won't keep you up at night.
Financing Professional Mortuary Equipment Purchases
When it comes to paying for that new walk-in cooler or embalming station, you have more options than you might think. Let me walk you through them.
Traditional equipment loans remain one of the most popular choices for major purchases. Many funeral directors don't realize that equipment-specific loans often come with better terms than general business loans. Why? Because the equipment itself serves as collateral, which typically results in lower interest rates. These loans generally range from 3-7 years, though our premium refrigeration systems at American Mortuary Coolers often qualify for terms up to 10 years because lenders recognize their exceptional durability.
"I was pleasantly surprised by the favorable terms we received on our cooler financing," shared a funeral director from Tennessee. "The local bank understood the long-term value of quality equipment and offered us a rate that made the decision easy."
Equipment leasing provides a flexible alternative to outright purchases. Many of our clients appreciate how leasing preserves their capital while still giving them access to top-quality equipment. Operating leases typically feature lower monthly payments but return to the lessor at the end of the term, while capital leases include ownership options when the lease ends. We've noticed increasing interest in lease programs that include maintenance coverage, creating predictable monthly expenses without surprise repair costs.
A funeral home director in Atlanta recently told us, "The predictable monthly payment on our leased walk-in cooler helps tremendously with cash flow management. Plus, knowing maintenance is covered gives us one less thing to worry about in an already demanding profession."
Don't overlook the tax advantages that can significantly reduce your actual equipment costs. Section 179 deductions allow immediate expensing of qualified purchases, while bonus depreciation provides additional first-year write-offs. For energy-efficient refrigeration systems like ours, you might also qualify for utility rebates or special tax incentives. These benefits can dramatically change the total cost picture when comparing different financing options.
At American Mortuary Coolers, we understand that funeral businesses have unique cash flow patterns. That's why we've developed several financing solutions designed specifically for funeral professionals. We offer promotional periods with 0% interest for qualified buyers, deferred payment options that allow installation now with payments beginning later, and even step-up payment structures with lower initial payments that increase as the equipment generates returns for your business.
"Our financing programs are built around one simple idea," explains our financing director. "New equipment should help your business thrive, not create financial stress."
When evaluating your options, look beyond the monthly payment to consider the total cost of ownership. Energy efficiency savings from our advanced cooling systems often justify higher initial investments. Similarly, our durable designs require less frequent maintenance, creating additional long-term value. Equipment that improves your operational efficiency brings value beyond the physical asset itself.
We're always happy to help our clients develop comprehensive cost analyses that include all these factors. After all, purchasing professional mortuary equipment isn't just about acquiring physical assets—it's about investing in your ability to serve families with dignity and efficiency for years to come.
More info about financing options for mortuary equipment
The right financing approach depends on your specific situation. Some funeral homes benefit most from traditional ownership, while others find leasing aligns better with their business model. We're here to help you steer these options and find the solution that brings you peace of mind along with quality equipment.
Environmental Considerations in Production and Disposal of Mortuary Equipment
The funeral industry is increasingly focusing on sustainability, and the environmental impact of professional mortuary equipment has become an important consideration for many funeral homes. From how equipment is manufactured to what happens when it's no longer usable, these environmental factors matter both for regulatory compliance and for funeral homes wanting to reduce their ecological footprint.
Sustainable Manufacturing Practices
When we build our coolers at American Mortuary Coolers, we think carefully about our environmental impact. The days of manufacturing without considering ecological consequences are behind us.
Most quality equipment manufacturers now use recycled metals whenever possible, especially for stainless steel components. This significantly reduces the environmental impact compared to mining and processing new materials. Our production facilities are designed with energy efficiency in mind - we've invested in equipment that uses less electricity while maintaining precision and quality.
Water conservation has become another priority in our manufacturing process. We use closed-loop cooling systems that recycle water rather than constantly drawing fresh supplies. This approach not only saves water but also reduces the energy needed to process and pump it.
"We've reduced our water usage by nearly 40% in the last five years," shares our production manager. "It's good for the planet and good for our bottom line too."
Our cutting and fabrication techniques are designed for minimal waste generation. Computer-controlled cutting ensures we maximize material use, and any scrap metal is recycled rather than sent to landfills. We've also shifted to more environmentally friendly finishing processes that reduce harmful emissions while still providing the corrosion resistance our products need.
Refrigerant Considerations
Refrigeration systems present unique environmental challenges, and this is an area where we've made significant improvements in recent years.
The industry has moved away from refrigerants like R-22 that damage the ozone layer. These ozone-depleting substances are being phased out globally under international agreements. Today's systems use alternatives with much lower environmental impact.
We carefully evaluate refrigerants based on their global warming potential (GWP) - a measure of how much heat a gas traps in the atmosphere compared to carbon dioxide. "Our current cooling systems use refrigerants with GWP ratings 99.9% lower than systems from just a decade ago," explains our engineering director. "It's one of the most significant environmental improvements we've made."
Preventing refrigerant leaks is another environmental priority. Our coolers feature advanced design and construction techniques that minimize the risk of refrigerant escaping. When equipment does need servicing, we provide detailed guidelines for proper refrigerant recovery to ensure these chemicals don't end up in the atmosphere.
We're also exploring emerging technologies like CO2-based refrigeration systems that have minimal climate impact. While these systems aren't yet standard across the industry, they represent the future direction of environmentally responsible cooling.
Energy Efficiency During Operation
The biggest environmental impact of mortuary equipment comes from its day-to-day operation over many years. This is why energy efficiency is so crucial.
High-quality insulation makes an enormous difference in energy consumption. Our coolers use insulation with superior R-values, creating an effective barrier that keeps the cold air in and warm air out. This directly translates to lower electricity usage and reduced environmental impact.
Modern variable-speed compressors represent another significant advancement. Unlike older units that simply turn on and off, these smart systems adjust their operation based on actual cooling needs, using only the energy required at any given moment.
"After upgrading to American Mortuary Coolers' energy-efficient system, our funeral home in Phoenix saw our electricity bill drop by nearly 40% during the summer months," shares one satisfied customer. "In Arizona's heat, that's a substantial saving both financially and environmentally."
Smart controls further optimize energy use by adapting cooling based on actual conditions rather than running at a constant rate. LED lighting in our units consumes far less electricity than fluorescent alternatives while generating less heat - a double benefit for refrigeration systems.
Regular maintenance keeps systems running at peak efficiency. A well-maintained cooler might use 15-25% less energy than one that's neglected, which is why we provide detailed maintenance guidelines with all our equipment.
Materials Selection for Longevity
Equipment that lasts longer creates less environmental impact - it's that simple. When a cooler serves for 20+ years instead of needing replacement after 7-10 years, the environmental benefits are substantial.
We use corrosion-resistant materials throughout our coolers to prevent deterioration that might lead to premature replacement. Our stainless steel is specifically chosen for its ability to withstand the demanding conditions of mortuary environments.
Our modular design approach allows for component replacement rather than entire system disposal when parts eventually wear out. This significantly extends the useful life of the equipment while reducing waste.
We design our systems to be upgradeable, allowing new technology to be incorporated without complete replacement. As refrigeration technology continues to improve, this approach ensures our customers can benefit from advancements without the environmental impact of manufacturing entirely new units.
"The most environmentally friendly equipment is the equipment you don't need to replace," notes our product development manager. "That's why we design for a minimum 20-year service life, well beyond industry averages."
End-of-Life Considerations
Eventually, all equipment reaches the end of its useful life. How it's handled at this stage makes a significant difference environmentally.
Our coolers are designed with recyclability in mind. We use construction methods that facilitate material recovery, making it easier to separate different components for appropriate recycling. The stainless steel that forms the majority of our units is 100% recyclable, creating a closed-loop material cycle.
We provide comprehensive decommissioning guidelines with all our equipment, ensuring proper handling at end-of-life. This includes specific instructions for managing refrigerants and electronic components that require special handling.
For certain components, we offer take-back programs to ensure proper recycling or disposal. This approach provides our customers with confidence that their old equipment won't create environmental problems down the line.
Some of our older units have found second lives through refurbishment programs. While not all equipment can be remanufactured, this approach provides additional value and extends the environmental benefits of the original manufacturing investment.
Regulatory Compliance and Certification
Environmental regulations increasingly affect equipment throughout its lifecycle, and staying compliant requires ongoing attention.
Energy Star certification is available for qualifying refrigeration equipment, providing third-party verification of energy efficiency. Similarly, RoHS compliance ensures restrictions on hazardous substances in electronic components are followed.
International agreements like the Montreal Protocol regulate ozone-depleting substances, while the Kigali Amendment focuses on phasing down high-GWP refrigerants. Our compliance team stays current with these evolving regulations across all regions we serve.
Local disposal regulations vary significantly, creating a complex landscape for equipment handling at end-of-life. We help our customers steer these requirements to ensure proper management of their older equipment.
At American Mortuary Coolers, we believe that environmental responsibility and business success go hand in hand. By creating durable, efficient equipment that minimizes ecological impact, we provide better value to our customers while protecting the planet we all share.
More info about mortuary equipment suppliers
Support Services: Installation and Maintenance by Suppliers
The relationship between equipment suppliers and funeral establishments doesn't end with purchase and delivery. Comprehensive support services ensure professional mortuary equipment performs optimally throughout its operational life, maximizing return on investment while minimizing disruptions.
Professional Installation Services
Proper installation establishes the foundation for equipment performance and longevity. At American Mortuary Coolers, we believe the way your equipment starts its life with you matters tremendously.
Before your new equipment even arrives, our team provides detailed site preparation guidance to ensure your space is ready. We've seen how proper planning prevents those last-minute scrambles that can throw off your schedule. Our delivery coordination team works like clockwork to ensure your equipment arrives when promised – because we understand you're running a business that can't afford unnecessary downtime.
"Installation quality directly impacts equipment performance and lifespan," explains our installation manager at American Mortuary Coolers. "Our certified installation teams have completed specialized training for each equipment type we offer."
When our professionals arrive, they don't just drop off equipment and leave. They handle expert positioning and leveling, make all necessary utility connections to electrical, plumbing, and ventilation systems, and conduct thorough testing of every function. We won't consider the job done until your staff receives hands-on training on proper operation and maintenance.
For complex installations like walk-in coolers, we provide detailed pre-installation checklists and coordinate closely with your staff and other contractors. Our goal is simple – minimize disruption to your ongoing operations while ensuring everything is set up perfectly from day one.
Preventive Maintenance Programs
Think of regular maintenance as health check-ups for your equipment – preventing costly failures and extending equipment life. Our TotalCare maintenance programs offer several tiers of coverage to fit your specific needs and budget.
During scheduled service visits, our technicians don't just glance at your equipment – they perform comprehensive inspections and make adjustments to optimize performance. They'll proactively replace wear items before they fail and conduct professional-grade cleaning of critical components. After each visit, you'll receive detailed service records for your files, which proves invaluable during regulatory inspections.
A funeral director from New York told us, "The quarterly maintenance program has eliminated unexpected downtime completely—the technicians catch and address small issues before they become problems." This preventive approach saves both money and headaches in the long run.
Emergency Repair Services
Even with the best preventive care, emergencies sometimes happen. When they do, you need support – fast. That's why American Mortuary Coolers maintains service technicians across all our service regions, ensuring prompt response when critical situations arise.
Our emergency support is available 24/7 because we understand that refrigeration issues don't conveniently occur during business hours. When you call, you'll reach a real person who understands the urgency of your situation. Our emergency response time averages under 4 hours nationwide, with many locations receiving same-day service.
We maintain an extensive inventory of replacement parts, allowing our technicians to complete most repairs in a single visit. If a permanent repair requires special ordering, we'll implement temporary solutions to keep your operation running. After resolving the immediate issue, we conduct a thorough root cause analysis to prevent similar problems in the future.
Remote Monitoring and Diagnostics
Modern technology has transformed how we support our equipment. Advanced remote monitoring systems act like a constant watchful eye on your critical systems, particularly refrigeration units.
"Our remote monitoring service detected a gradual temperature increase in a funeral home's walk-in cooler," recalls our service director. "We dispatched a technician who identified and replaced a failing compressor component before any noticeable performance issues occurred, preventing a potential emergency situation."
These systems continuously track refrigeration performance and send automated alerts the moment parameters deviate from normal. Our technicians can then evaluate system performance remotely, often diagnosing issues without requiring an immediate site visit. The predictive analytics built into our monitoring platforms can identify potential failures before they occur, allowing for scheduled maintenance rather than emergency repairs.
Many of our clients tell us this technology provides tremendous peace of mind, especially during holidays or weekends when staff may be limited.
Staff Training and Support
The value of your equipment depends heavily on proper operation. We've found that comprehensive staff training pays dividends in equipment longevity and performance.
During installation, we provide initial hands-on training for your team. But we understand that staff changes occur, so we offer refresher sessions whenever you need them. Beyond basic operation, we provide advanced guidance to help you maximize your equipment's capabilities and troubleshooting instruction that empowers your staff to address minor issues.
We've created both written materials and video tutorials that remain accessible 24/7 through our online knowledge base. Whether your team prefers in-person learning or self-guided instruction, we accommodate different learning styles and scheduling needs.
Warranty and Extended Coverage Options
Protection against unexpected issues provides genuine peace of mind for funeral establishments. Every piece of professional mortuary equipment from American Mortuary Coolers comes with standard warranty coverage, but many clients choose to improve their protection.
Our extended warranty options provide additional coverage beyond the standard period, while comprehensive service plans combine regular maintenance with repair coverage. We can create customized protection packages custom to your specific operational needs and even develop upgrade pathways that facilitate equipment updates as technology advances.
A funeral director from the Southwest Region shared, "The extended service plan for our refrigeration system has been invaluable. Knowing exactly what our equipment costs will be for the next five years allows for much more accurate financial planning."
This predictability helps funeral homes budget more effectively while ensuring their equipment receives the care it needs to perform reliably year after year.
More info about mortuary equipment suppliers
Frequently Asked Questions about Professional Mortuary Equipment
What are the most essential pieces of professional mortuary equipment?
When setting up a funeral establishment, certain equipment forms the backbone of your operations. At American Mortuary Coolers, we're often asked what truly matters most.
Refrigeration systems stand as the absolute foundation for any funeral operation. Whether you're considering a walk-in cooler for higher volume facilities or a drawer system for more limited space, proper body preservation before preparation is non-negotiable. This is where our expertise truly shines, as we custom-design refrigeration solutions to match your specific needs.
Embalming stations represent another critical investment. Quality preparation tables should feature 304-grade stainless steel construction – not just for durability but for proper sanitation. The best stations include integrated drainage systems, convenient instrument trays, and connections for ventilation systems. As one Tennessee funeral director told us, "My embalming station is where I spend most of my working hours – investing in quality here makes every day easier."
Body lifts and transport equipment have evolved significantly in recent years. Modern hydraulic and battery-powered systems now make it possible for a single staff member to safely manage transfers that once required multiple people. When selecting this equipment, capacity ratings matter – look for minimum 600-pound capacity, with bariatric options if your community demographics require it.
Preparation room ventilation directly impacts both staff health and regulatory compliance. OSHA standards recommend a minimum of 12 air changes per hour in preparation areas. Beyond compliance, proper ventilation creates a more comfortable working environment and demonstrates your commitment to staff wellbeing.
Dressing tables complete the essential equipment list. While sometimes overlooked, these specialized surfaces for final preparation need fluid-resistant materials and ergonomic working heights to prevent staff strain during those final, crucial preparation steps.
"While every funeral home has unique needs based on case volume and service types," our equipment specialist explains, "these five categories form the foundation that supports everything else you do."
How does the quality of mortuary equipment affect funeral services?
The connection between equipment quality and service excellence runs deeper than many realize. Though families rarely see behind the scenes, professional mortuary equipment impacts every aspect of the funeral experience.
Presentation quality stands as the most visible impact. Superior equipment enables your preparation staff to achieve better results, directly affecting how the deceased appears during viewings. As a funeral director from Georgia recently shared with us, "When I'm not fighting with inadequate equipment, I can focus completely on the artistic elements that bring comfort to families."
Equipment reliability translates directly to service reliability. When a refrigeration system fails or an embalming station develops issues, the ripple effects can disrupt multiple families' services. The peace of mind that comes from dependable equipment allows your staff to focus entirely on caring for the living while honoring the dead.
Staff efficiency improves dramatically with quality equipment. Well-designed systems reduce physical strain and streamline processes, allowing your team to dedicate more attention to personalized service elements. We've had customers report that after upgrading to our ergonomic systems, their staff experienced less fatigue and could maintain higher standards throughout the day.
Regulatory compliance becomes far simpler with properly designed equipment. Quality systems typically incorporate features that ensure compliance with health regulations and OSHA requirements by design, rather than requiring workarounds or additional steps.
Perhaps most importantly, when equipment performs reliably, it creates the foundation for excellence in all other aspects of service. A funeral director from North Carolina summed it up perfectly: "Families never see our preparation room or cooler, but they absolutely experience the difference quality equipment makes in our ability to serve them."
What should I look for in a mortuary equipment supplier?
Finding the right equipment partner involves looking beyond just price and product specifications. At American Mortuary Coolers, we believe several factors distinguish truly valuable suppliers from mere vendors.
Industry experience matters tremendously. The funeral profession has unique requirements that general equipment manufacturers often misunderstand. Suppliers who specialize exclusively in funeral industry equipment bring valuable insights to every project. When evaluating potential partners, ask how long they've focused specifically on mortuary equipment – not just general commercial equipment.
Manufacturing quality determines how your equipment will perform over decades of use. Ask detailed questions about materials (like the grade of stainless steel used), construction methods, and quality control processes. At American Mortuary Coolers, we're proud to show customers exactly how our units are built and the quality standards we maintain.
Customization capabilities often separate the best suppliers from the adequate ones. Your facility has unique spatial constraints and operational needs that standard, one-size-fits-all equipment might not address. A supplier willing to tailor solutions specifically for your space and workflow demonstrates both flexibility and commitment to your success.
Installation expertise significantly impacts equipment performance. Professional installation by factory-trained technicians – not subcontracted to general contractors – ensures your equipment operates as designed from day one. We've seen too many cases where excellent equipment performed poorly due to improper installation.
Service network availability provides peace of mind for years to come. Before committing to a supplier, verify their service coverage in your specific location. Ask about response times, parts availability, and whether they offer preventive maintenance programs to avoid emergency situations.
Customer references offer valuable insights into the real-world experience of working with a supplier. Ask for references from facilities similar to yours, and specifically inquire about long-term reliability and service responsiveness. At American Mortuary Coolers, we're happy to connect prospective customers with existing clients who can share their experiences.
Financial stability ensures your supplier will be there to honor warranties and provide ongoing support. Research the company's history and stability before making a major equipment investment. As one funeral director wisely noted, "When you buy equipment expected to last 20+ years, you need a company that will be around just as long."
"The relationship with your equipment supplier often spans decades," our customer relationship manager explains. "Taking time to evaluate these factors helps ensure you're selecting a true partner in serving families, not just a vendor selling products."
Conclusion
The landscape of professional mortuary equipment continues to evolve, bringing exciting advancements that transform how funeral professionals care for the deceased and serve grieving families. When we look at how far mortuary technology has come—from basic wooden tables to sophisticated refrigeration systems with remote monitoring—it's clear that quality equipment forms the backbone of exceptional funeral service.
At American Mortuary Coolers, we've had the privilege of witnessing how the right equipment makes all the difference. From busy funeral homes in New York City to small-town establishments in rural Texas, we've seen directors breathe a sigh of relief when their new equipment arrives and works exactly as promised. There's something deeply satisfying about providing tools that help professionals deliver dignified care during life's most difficult moments.
Choosing the right professional mortuary equipment isn't just about checking boxes on a specification sheet. It's about finding solutions that complement your unique space, workflow, and service philosophy. The equipment in your preparation room silently communicates your values—your commitment to excellence, your respect for the deceased, and your dedication to supporting your staff.
We believe that quality never goes out of style. While trends may come and go, the fundamentals remain: durable construction, thoughtful design, reliable performance, and responsive support. That's why we build every American Mortuary Cooler with meticulous attention to detail, using materials that stand the test of time and craftsmanship that reflects our Tennessee roots.
What sets us apart isn't just what we build, but how we build it—and why. Every cooler, every piece of equipment represents a partnership between our team and yours. We listen first, design second, and stand behind our work for the long haul. From Georgia to California, from Illinois to South Carolina, our customers become part of our extended family.
The funeral profession faces unique challenges that require specialized solutions. That's why we focus exclusively on serving funeral professionals—because we understand your world and the critical importance of the work you do every day. When you choose American Mortuary Coolers, you're not just getting equipment; you're gaining a partner who speaks your language and shares your commitment to excellence.
More info about American Mortuary Coolers
Contact American Mortuary Coolers today to discuss your professional mortuary equipment needs. Let us show you how our custom solutions can improve your facility's capabilities while ensuring the highest standards of dignity and care. From Pennsylvania to Texas, we deliver quality directly to your door—because we believe distance shouldn't stand between you and exceptional equipment.